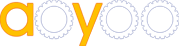
ASSURANCE
1. Welding a system frame: Welding structure, stronger stability and rigidity, not easy to deform during the moving process
2. Tool quick change module: the universal tool holder can be combined with the tool arbitrarily to realize the quick and convenient tool replacement of different materials
3. Complete tool categories: milling cutters, vibrating knives, bevel cutters, drag knives, press wheels, pneumatic knives, electric round knives, etc., different tools for cutting different materials
4. Honeycomb aluminum countertop: durable without deformation, vacuum adsorption design, super strong wind, strong suction (partition adsorption is possible, small sample adsorption is no longer difficult)
5. Countertop felt: using imported materials, good air permeability, abrasion resistance, long service life, minimize customer use costs
6. Strict dust-proof design: reduce equipment failure rate and extend equipment use time
7. Four-corner emergency stop switch: safety protection function, in case of miscutting, the four-corner emergency stop switch can be forced to shut down to reduce loss
8. Anti-interference: Taking into account the complex electromagnetic environment factors actually used by the customer, an anti-interference operation screen is specially configured, which will not be affected by the surrounding electronic environment during work, and will not flicker the screen
9. Safe operating environment: infrared automatic induction safety device ensures the maximum protection of the operator during the high-speed movement of the machine, while avoiding the loss of cutting materials
10. Unwinding device: Unwinding device is provided, which can ensure that the material is cut smoothly and softly during the coil conveying process. Different unwinding heights can be set according to different characteristics and specifications of the coil, thereby improving the output and quality of cutting.
11. Table compensation function: The flatness of the table is detected by a high-precision distance detector, and the plane is corrected in real time by software to achieve a perfect cutting effect.
12. Control system: adopts high-performance multi-axis motion control system, which is easy to maintain, low cost, and provides personalized development services
13. Working mode: Servo motor is used to drive the screw control mode, and the computer can be linked with the computer to preset and store the knife deep knife pressure according to different needs
14. Graphic design software integration: it can be docked with ArtiOSCAD, AutoCAD, Coreldraw and other software to simplify the structure and work flow of graphic designers
15. Over-cutting optimization: The self-developed CAM software is used to systematically optimize the physical over-cutting phenomenon of the tool, to restore the graphic outline to the greatest extent, and to bring customers the perfect cutting effect
16. Positive and negative cutting: Combine the boundary recognition function to quickly identify and locate the material boundary, and realize the positive and negative graphic cutting
17. Data interface: network interface, can realize remote upgrade and maintenance, the transmission speed is fast and the distance is long, and it can be transmitted with multiple computers at the same time.
18. Automatic identification of material thickness: automatic detection of the thickness of the material, no need to manually measure and then record the thickness data to the software
If you want to know more about performance issues, please leave a message , we will have a professional staff contact you.
AOYOO Media
E-mail:info@aolcnc.com
phone:+86-18560162709
WhatsApp /微信:+8618560162709
youtube:https://www.youtube.com/channel/UCctbMXFvompG-41Wecb1mpw
website:https://www.aoyoocut.com/
Facebook:https://www.facebook.com/AOYOOCUTTER