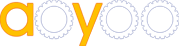
ASSURANCE
One company employing AOYOO carbon fibre seat cutting machine is a supplier of automotive interior systems and filters. The company produces complete systems that include seats, door trim, ceiling material, and carpeting.
As manufacturers seek to meet customers' demands for quiet, comfortable, stylish interiors, car seat systems have become complex and more difficult to manufacture. New features such as occupant detection systems, seat heating and cooling systems, and entertainment systems are now built into seats. Product development schedules have also shortened—the time between initial concept and prototype is now approximately four weeks, or about half of what it was just a few years ago. In the past, the company developed prototypes by digitising foam seat shapes and developing patterns, which were then hand-cut from leather, vinyl or other materials. This was time consuming and lacked the accuracy required to meet the automotive industry's stringent tolerances. Cutting a single trim cover could take two to three hours. The company looked for a cutting solution that would enable engineers to accelerate prototyping and ensure that the patterns developed would work the same in production as they did in prototyping. After evaluating several cutting solutions, it chose AOYOO carbon fibre seat cutting machine.